ACES Project: Advancing Additive Manufacturing with printed electronic Sensors
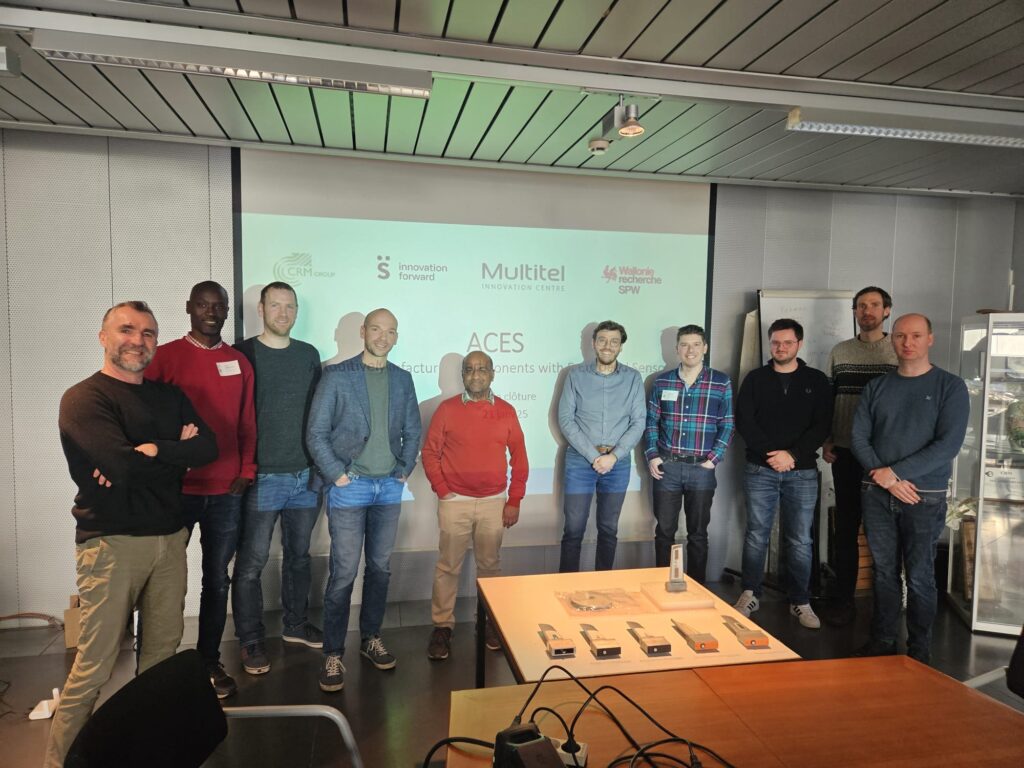
The ACES (Additively Manufactured Components with Embedded Sensors) project, funded by Win4Collective (Wallonia Region), has successfully reached completion at CRM Group. This project focused on an emerging challenge in additive manufacturing: how to integrate smart sensors directly onto 3D-printed metallic components to enable real-time structural health monitoring.
The project specifically targeted Selective Laser Melting (SLM), a widely used 3D printing technique for metal parts. While SLM offers significant advantages in producing complex geometries, it also introduces high surface roughness and porosity, which can make functionalization more difficult. The ACES project set out to overcome these limitations by developing advanced surface treatment and open a new route of 3D printed electronic manufacturing for sensor integration.
From 3D Printing to Smart Components: The ACES Approach
The main objective of ACES was to demonstrate the feasibility of directly integrating printed sensors onto SLM-produced metal components, particularly for use in high-temperature and high-performance environments.
💡 Why is this important?
✔ Traditional sensors often require additional assembly steps, which can weaken component integrity and increase manufacturing costs.
✔ Direct sensor printing enables real-time health monitoring and predictive maintenance, reducing downtime and operational risks.
✔ Integrating smart sensors into complex 3D-printed components opens the door for new applications in aerospace, energy, and advanced manufacturing.
Technical Achievements of the ACES Project
During the project, CRM Group successfully developed and validated multiple sensor integration techniques, making 3D-printed metal components “smart” by embedding various types of functional sensors.
🔹 Surface Preparation & Sensor Printing
One of the key challenges was modifying the rough and porous SLM-produced surfaces to make them suitable for sensor deposition. CRM Group developed plasma spray coatings and masking techniques to create electrically isolated sensor layers while maintaining mechanical integrity.
🔹 High-Temperature Sensor Integration
Several types of functional sensors were successfully printed onto SLM-fabricated components:
- Thermocouple Sensors (TC): NiCr-NiAl-based temperature sensors were directly printed on turbine blade structures, enabling accurate temperature monitoring up to 1000°C.
- Resistance Temperature Detection (RTD) Sensors: Integrated for precise temperature control.
- Strain Sensors: Designed for monitoring mechanical stress and deformation in real-time.
- Radio Frequency Identification (RFID) Sensors: Embedded for wireless tracking and component identification.
🔹 Wireless Monitoring with IoT
To enhance the functionality of printed sensors, the ACES project partnered with MultiTel to develop an IoT-enabled electronic circuit. This system enables wireless data transmission and remote health monitoring of industrial components. A cavity was designed into 3D-printed turbine blades to house this circuit, allowing real-time performance tracking and predictive maintenance.
Future Applications & Industrial Impact
The successful completion of ACES marks an important step toward smart manufacturing, where industrial components will be able to monitor their own structural health. The ability to embed real-time monitoring sensors into 3D-printed metal parts has far-reaching implications:
✅ Aerospace & Energy Industries – Improved monitoring of high-temperature turbine blades and critical metal components, leading to better reliability and efficiency.
✅ Predictive Maintenance – Integrated sensors enable real-time diagnostics, reducing maintenance costs and preventing failures before they occur.
✅ Advanced Manufacturing – Combines additive manufacturing with functional electronics, paving the way for next-generation industrial components.
What’s next?
At CRM Group, we continue to explore new frontiers in additive manufacturing and smart materials. By leveraging 3D printing, functional coatings, and IoT-enabled sensors, we are developing next-generation industrial solutions for the future of smart manufacturing.
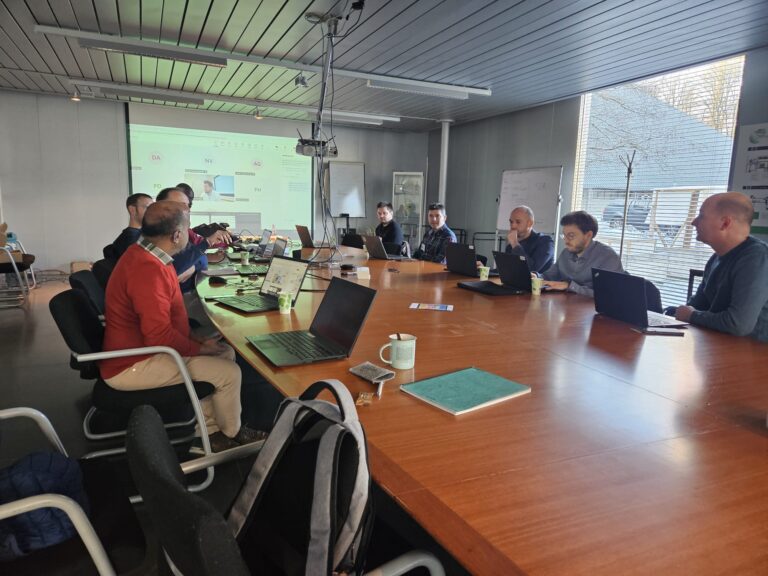