Burwear
Modelling and reduction of back-up roll wear in cold and temper mils (BURWear)
Objectives
To study the degradation mechanism(s) of BURs in industrial plants by offline macroscopic and microscopic surface analysis at Tata Steel’s roll shop before grinding:
- To study/simulate the degradation phenomena on the 2D/3D rolling simulator at CRM
- To evaluate new roll grades on the 2D/3D rolling simulator
- To develop an innovative system to measure BUR profiles inside a mill stand between two coils or during work roll changes with an aimed precision of at least <5 μm and preferably close to 1 μm
- To install the new innovative measurement system in an industrial stand
- To acquire and analyze the BUR profile evolution during at least 3 BUR campaigns
- To define the degradation mechanism of BUR rolls in cold rolling operations
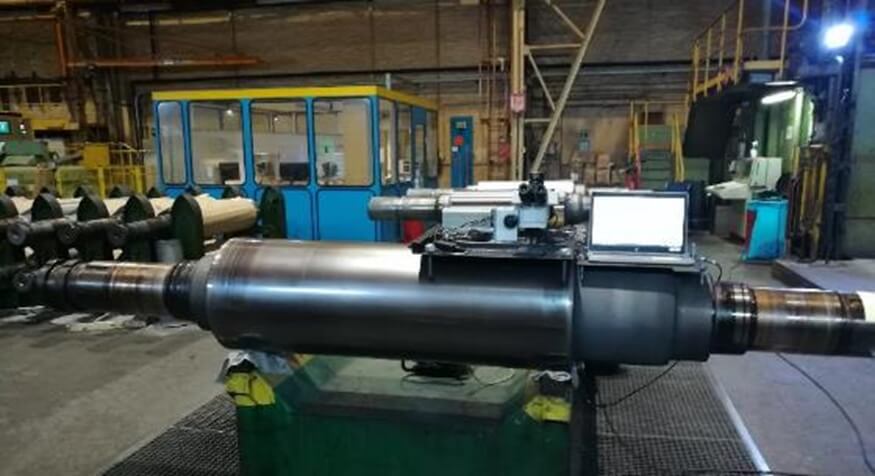
Description
The performance of Back-Up Rolls (BURs) in flat rolling mills has a major impact on the rolling process stability, the strip shape, mill productivity and production costs. The main limiting factors in roll performance are wear and Rolling Contact Fatigue (RCF), typically manifested as ‘work hardening’ and eventually ‘crumbly spalls’ (see Figure). Wear rates and resulting BUR wear profiles are usually not understood and (thus) not well predicted. In order to get a better understanding and prediction of back-up roll degradation and wear a European RFCS project has been started “BURWEAR” with as partners Tata Steel, CRM, Gontermann-Peipers (GP) and the University of Twente (UT). The project plan has been organized in 8 work packages (WPs).
Partners
Funding Bodies
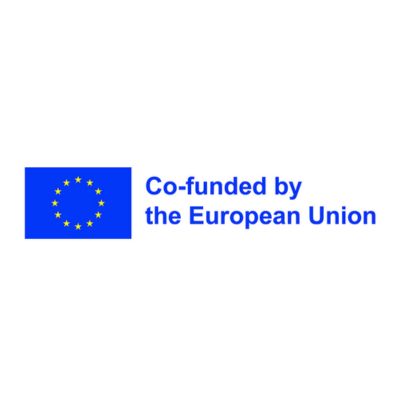
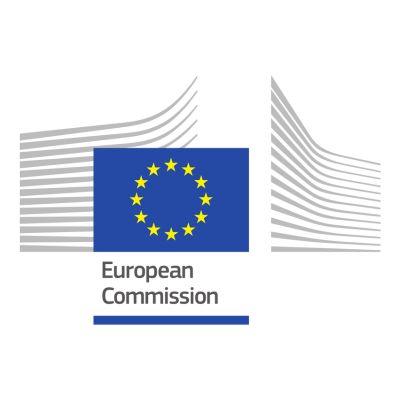
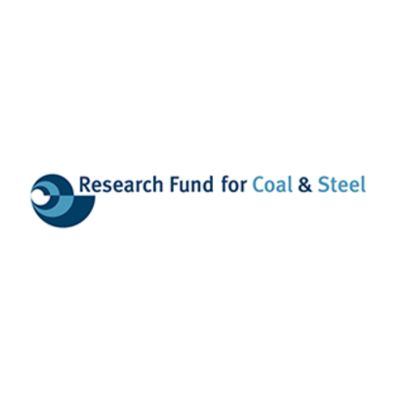